Guruprasad Bangle
Chief Technical Officer (CTO), SolutionBuggy
Imagine a conveyor belt overflowing with a vibrant mix of fruits and vegetables. Some are perfectly ripe and ready for the grocery store, while others might be a little underripe or show a few blemishes. How do food manufacturers ensure only the best quality produce reaches your plate? This is where the magic of food sorting and palletizing comes in!
Sorting the Good from the Not-So-Good: The Art of Food Sorting
Food sorting is the process of separating food items based on pre-defined criteria. Think of it as a quality control checkpoint where only the finest cut (pun intended!). There are several ways to achieve this:
- Manual Sorting: The classic method involves trained personnel visually inspecting and manually picking out items that don’t meet the quality standards. While reliable for certain applications, it can be time-consuming and labor-intensive.
- Color Sorting: Modern technology plays a starring role in automated sorting. Color sorting machines use high-resolution cameras and sophisticated algorithms to identify and separate food items based on color variations. This ensures consistency in ripeness, detects blemishes, and eliminates foreign objects.
- Size and Shape Sorting: Ever wondered how those perfectly round oranges or uniform green beans end up in your shopping cart? Optical sorting machines can also differentiate objects based on size and shape, ensuring consistent presentation and optimizing packaging efficiency.
- Weight Sorting: For some products, weight is a crucial quality indicator. Weight sorting technology ensures consistent portion sizes and helps prevent underfilling or overfilling of packages.
- X-Ray Sorting: This advanced technique utilizes X-rays to detect internal defects, foreign materials like metal or plastic fragments, and even internal structures like pits in fruits.
Building Blocks of Stability: The Power of Palletizing
Once sorted and deemed worthy, food items need to be efficiently organized and stacked for transportation and storage. This is where palletizing takes center stage!
- The Palletizing Process: Food products are arranged in a stable and secure configuration on a pallet, a flat wooden or plastic platform. This methodical stacking ensures efficient use of space during storage and transportation, minimizing the risk of damage or spoilage.
- Manual Palletizing: Similar to manual sorting, this involves workers physically placing food items onto pallets. It’s a viable option for small-scale operations but can be physically demanding and prone to human error.
- Robotic Palletizing: Robots have become the champions of the palletizing arena. Programmable robotic arms can lift, stack, and arrange food items with precision and speed, significantly reducing labor costs and ensuring consistent palletization patterns.
Technological Advancements: A Glimpse into the Future
The food sorting and palletizing landscape is constantly evolving, driven by technological advancements.
- Artificial Intelligence (AI): AI-powered systems are learning to analyze visual data with even greater accuracy, enabling the detection of subtler quality variations and facilitating more precise sorting decisions.
- Machine Learning (ML): Machine learning algorithms are continuously adapting and improving their sorting capabilities based on real-time data. This allows for more accurate product classification and identification of even the most minor defects.
- Vision Systems with Deep Learning: Deep learning algorithms are enhancing the capabilities of vision systems used in sorting. These systems can learn and identify a wider range of quality parameters, ensuring a more comprehensive and nuanced quality control process.
- Cobots (Collaborative Robots): These user-friendly robots are designed to work safely alongside human workers. Cobots can be particularly useful in palletizing tasks, assisting with heavy lifting and repetitive tasks, while human workers oversee the overall process.
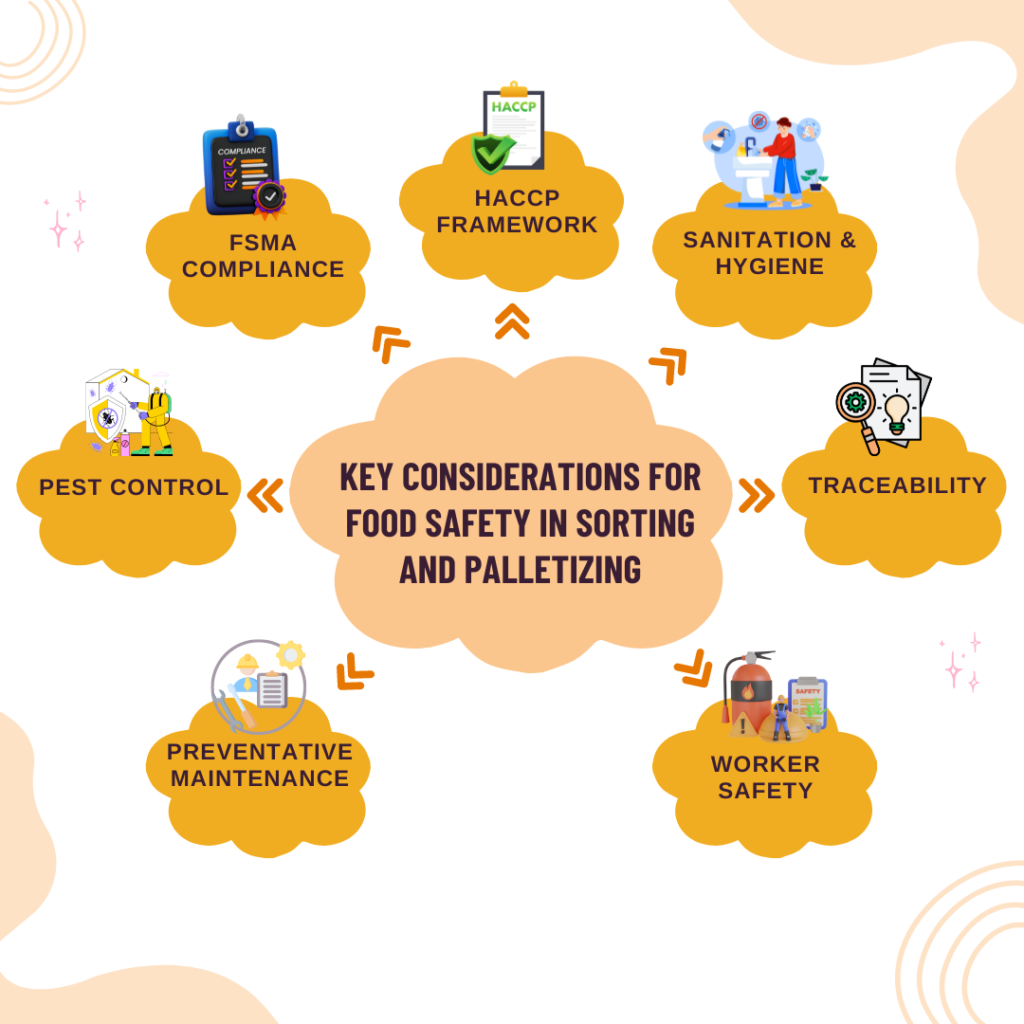
Safety First: Regulatory Considerations for Food Sorting and Palletizing
Food safety remains paramount throughout the entire manufacturing process. Here are some key regulations and considerations:
- Food Safety Modernization Act (FSMA): This US regulation emphasizes preventive controls throughout the food supply chain, including sorting and palletizing operations. Sanitation procedures, equipment maintenance, and personnel training are crucial aspects.
- Hazard Analysis and Critical Control Points (HACCP): This globally recognized framework helps identify potential food safety hazards and implement effective control measures. This ensures food sorting and palletizing practices minimize risks of contamination or product degradation.
- Sanitation & Hygiene: Maintaining a clean and hygienic environment is essential. Regular cleaning and disinfection of sorting and palletizing equipment, as well as proper handling practices, are crucial to prevent the spread of foodborne illnesses.
- Traceability: The ability to track food products throughout the supply chain is critical for addressing potential recalls or identifying the source of contamination. Sorting and palletizing procedures should be designed to ensure proper traceability by:
- Maintaining clear product identification: Implementing a robust system for labeling and coding products at each stage of sorting and palletizing. This allows you to track specific batches of food items if necessary.
- Record-keeping: Maintaining accurate records of sorting and palletizing activities, including dates, times, and personnel involved. Additionally, records should document quality control checks and any identified defects.
- Integration with traceability systems: Exploring integration of sorting and palletizing equipment with electronic traceability systems. This allows for real-time data capture and facilitates efficient product tracking throughout the supply chain.
- Worker Safety: Implementing proper safety protocols to minimize the risk of injuries during sorting and palletizing operations. This includes providing workers with appropriate personal protective equipment (PPE) and training them on safe handling practices.
- Preventative Maintenance: Regularly maintaining and inspecting sorting and palletizing equipment is crucial to ensure optimal performance and prevent breakdowns that could compromise food safety.
- Pest Control: Maintaining a robust pest control program to minimize the risk of contamination by rodents, insects, or other pests in the sorting and palletizing area.
By adhering to these regulations and best practices, you can ensure that your food sorting and palletizing operations are not only efficient but also prioritize food safety at every stage.
Packaging: The Final Touch
Sorting and palletizing are crucial steps in the food manufacturing journey, but the story doesn’t end there. Packaging plays a vital role in protecting food items, preserving quality, and influencing consumer decisions. Here are some key considerations:
- Material Selection: The type of packaging material chosen depends on the specific food product, desired shelf life, and environmental impact considerations. Rigid plastic containers might be suitable for some products, while others may benefit from flexible film packaging.
- Package Design: Packaging design goes beyond aesthetics. It should be functional, providing adequate protection while ensuring clear labeling and proper food safety information. Sustainable packaging options made from recycled materials are becoming increasingly popular with environmentally conscious consumers.
- Integration with Sorting & Palletizing: Ideally, the sorting and palletizing systems should seamlessly integrate with the packaging line. This ensures smooth and efficient product flow from sorting and stacking to final packaging for distribution.
SolutionBuggy: Your Partners in Food Sorting and Palletizing Success
Navigating the complexities of food sorting and palletizing can seem daunting. But fear not, SolutionBuggy is here to be your trusted advisor on this journey! Our team of food processing experts can assist you in several ways:
- Needs Assessment & Solution Design: We work closely with you to understand your specific needs, product types, and production volume. Based on this analysis, we recommend the most suitable sorting and palletizing technologies for your operation.
- Equipment Selection & Implementation: Our team can guide you through the selection of appropriate equipment, considering factors like budget, product compatibility, and integration with existing systems. We can also assist with installation and commissioning of the chosen technology.
- Training & Skill Development: Our training programs equip your workforce with the necessary knowledge and skills to operate and maintain sorting and palletizing equipment effectively. This ensures efficient and safe operation, maximizing the value of your investment.
- Regulatory Compliance Guidance: Staying compliant with food safety regulations can be complex. SolutionBuggy provides guidance on relevant regulations like FSMA and HACCP, ensuring your sorting and palletizing practices meet all necessary standards.
- Continuous Improvement & Optimization: We believe in continuous process improvement. Our team of experts can analyze your sorting and palletizing operations to identify areas for optimization, ultimately increasing efficiency and minimizing product waste.
With SolutionBuggy by your side, you can navigate the complexities of food sorting and palletizing with confidence. We can help you select the right technology, ensure regulatory compliance, and ultimately empower you to deliver the freshest and highest quality food products to your consumers.
Let’s work together to build a more efficient and sustainable food manufacturing future! Contact SolutionBuggy today to discuss your food sorting and palletizing needs.