The global manufacturing landscape is undergoing a transformative shift, driven by automation and smart technologies. Industries are increasingly adopting robotic solutions to enhance efficiency, precision, and scalability. Automated systems streamline production, reduce dependency on manual labor, and ensure consistency in quality. With the rise of Industry 4.0, manufacturing units are integrating robotics, IoT, and AI-driven technologies to create connected and intelligent workflows.
India, as one of the fastest-growing industrial economies, is witnessing a rapid adoption of automation. The push for smart factories and digital transformation is being fueled by factors such as increasing labor costs, demand for higher productivity, and the need for error-free production. Sectors like automotive, pharmaceuticals, food and beverage, electronics, and logistics are actively investing in robotic automation to stay competitive. Palletizing, depalletizing, material handling, and packaging are among the key processes being automated to improve operational efficiency.
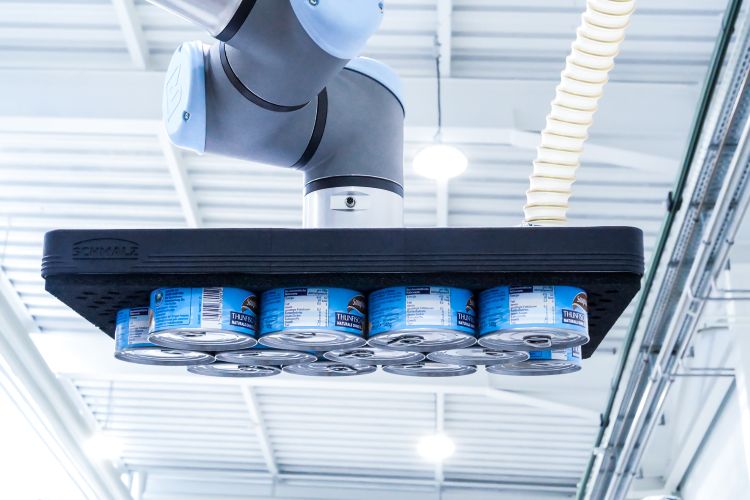
Lightweight Layer Grippers ZLW
How Automation Transforms Manufacturing
Integrating automation into manufacturing workflows brings multiple advantages. Increased production speed allows companies to meet growing market demands without compromising quality. Reduced labor dependency helps mitigate workforce shortages and minimizes fatigue-related inefficiencies. Enhanced workplace safety ensures that employees are not exposed to hazardous lifting tasks, preventing workplace injuries. Moreover, automation contributes to cost savings by reducing material waste, optimizing energy consumption, and lowering operational expenses.
However, automation is not just about robots replacing manual tasks—it is about enhancing collaboration between humans and machines. Human-Robot Collaboration is becoming a critical aspect of modern manufacturing, where lightweight robots and collaborative automation tools assist workers in repetitive and physically demanding tasks. This is where advanced gripping solutions play a crucial role in optimizing material movement across production lines.
Introducing the Lightweight Layer Gripper ZLW: A Smart Handling Solution
To fully leverage the benefits of automation, manufacturers require adaptable and efficient material handling tools. The Lightweight Layer Gripper ZLW from Schmalz is designed to optimize palletizing, depalletizing, and various intra-logistics processes with high precision and minimal effort. Its modular and lightweight design makes it ideal for cobots and smaller robotic systems, ensuring seamless integration into automated workflows.
This innovative gripper extends beyond palletizing to multiple production and packaging applications. It plays a critical role in logistics and warehousing, where it automates depalletizing and goods movement between different stages of packaging and distribution. In the food and beverage sector, it efficiently handles packaged goods such as cartons, jars, cans, and plastic-wrapped products while ensuring hygienic and damage-free transportation. The pharmaceutical industry benefits from its precision when handling medicine boxes, vials, and sterile packaged goods, meeting strict hygiene and safety standards. Additionally, it enhances consumer goods packaging through pick-and-place applications, transitioning items between production lines and final packaging. For automotive and manufacturing, the gripper facilitates line changeovers, transferring components between workstations, and moving finished products into storage or final packaging.
It is designed to accommodate a variety of handling requirements and is available in different sizes, ensuring suitability for diverse applications. Its lightweight aluminum construction minimizes the load on robots, maximizing efficiency. The gripper handles varying load capacities, making it suitable for both small and medium-sized workpieces while maintaining a secure grip on different materials. Customization options allow for adaptation to specific industry needs. The sealing elements come in two configurations—plug-in suction cups, ideal for uniform and stable surfaces, and sealing foam, which offers a secure grip on irregular or delicate items. An optional floating flange compensates for height variations within a layer, ensuring consistent performance. The vacuum system can be tailored to specific operational requirements, with options for external vacuum connection for high-power applications or an integrated vacuum generator for a compact, self-contained setup. Additionally, an optional rounded safety frame enhances protection in human-robot collaboration environments.
Handling Capabilities and Workpiece Variability
One of the key advantages of this solution is its ability to manage a broad spectrum of workpieces. It efficiently grips cardboard boxes, shrink-wrapped packages, plastic containers, metal cans, glass jars, and irregularly shaped products. The adaptable sealing options ensure a firm hold on both smooth and uneven surfaces, making it suitable for delicate as well as robust materials. This flexibility eliminates the need for frequent tool changes, optimizing workflow and productivity.
How It Works
Equipped with advanced vacuum technology, the gripper secures and transports workpieces with precision. Once mounted onto a robot or gantry system, it positions itself over the target layer. The vacuum system activates, generating negative pressure to ensure a strong grip. If a floating flange is included, it automatically adjusts to height variations for even gripping force. Once secured, the system smoothly transfers the workpieces to the desired location, whether for palletizing, line transitions, packaging, or production movement. The vacuum is then released efficiently, enabling seamless integration into automated workflows.
Optimizing Material Handling Beyond Palletizing
While widely used in palletizing and depalletizing, this gripper offers significant advantages in production line transitions, where it assists in moving products between workstations for line changeovers. It also plays a key role in transferring finished goods to packaging stations, ensuring a smooth workflow through the final stages of manufacturing. Additionally, it simplifies the handling of goods for packaging, speeding up the movement of items into cartons, crates, or wrapping machines. These capabilities make it an indispensable tool for modern automated manufacturing and logistics operations.
Key Advantages
This technology delivers multiple benefits that enhance usability and efficiency. Its lightweight structure reduces payload demands, making it ideal for collaborative robots and smaller automation systems. The modular configuration allows users to customize the gripper based on specific handling tasks, whether through different sealing elements, vacuum sources, or safety features. Energy efficiency is a standout feature, as optimized vacuum generation minimizes power consumption while maintaining superior gripping performance. Additionally, the high compatibility ensures easy integration with various robotic and automated systems, while safety-enhanced operation makes it suitable for HRC applications without compromising workplace safety.
With its flexibility, efficiency, and precision, this lightweight gripper streamlines material handling across production, packaging, and logistics. Its adaptability and customization enhance automation, boosting productivity, safety, and process reliability.
Schmalz India Private Limited